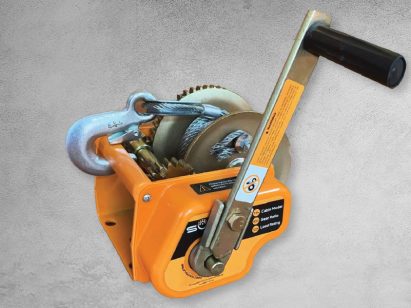
Top Tips on How to Maintance your Boat Trailer
Owning a boat opens up a world of…
🚛 Squeaks, grinds, and wobbles – these are the telltale signs of neglected trailer bearings, and they could be spelling disaster for your next journey. But here’s the kicker: most trailer owners don’t realize they’re sitting on a ticking problem until it’s too late.
Are you one of them? 🤔 Imagine this: You’re halfway through your long-awaited road trip when suddenly, your trailer starts behaving erratically. The smooth ride turns into a nerve-wracking ordeal, and before you know it, you’re stranded on the roadside. All because of one tiny, often overlooked component – your trailer bearings.
But fear not! We’re about to dive into the world of trailer bearing maintenance, unlocking the secrets to extending their life and ensuring your adventures remain uninterrupted. Visit our website to explore essential tools and products that make trailer maintenance a breeze. So buckle up and get ready to master the art of trailer bearing maintenance – your future self (and your wallet) will thank you!
Trailer bearings are crucial components in your trailer’s wheel assembly, playing a vital role in ensuring smooth and efficient movement. These small but mighty parts allow the wheels to rotate freely while supporting the weight of the trailer. Bearings reduce friction between the wheel hub and axle, preventing overheating and premature wear.
There are two main types of trailer bearings:
Type |
Advantages |
Best suited for |
---|---|---|
Roller bearings |
Higher load capacity, better for heavier trailers |
Large trailers, heavy-duty applications |
Ball bearings |
Smoother operation, less friction |
Smaller trailers, lighter loads |
Recognizing the symptoms of failing bearings is crucial for timely maintenance. Look out for these warning signs:
Regular inspection of trailer bearings is crucial for maintaining their longevity and ensuring safe towing. The frequency of inspection depends on several factors:
Here’s a general guideline for inspection intervals:
Usage |
Inspection Frequency |
---|---|
Light use |
Every 3-6 months |
Moderate use |
Every 2-3 months |
Heavy use |
Monthly |
After long trips |
After each trip |
When inspecting your trailer bearings, pay close attention to:
To perform a thorough bearing inspection, you’ll need:
Develop a comprehensive checklist to ensure consistent and thorough inspections:
By following this inspection routine, you’ll catch potential issues early, extending the life of your trailer bearings and ensuring safer towing experiences. Remember, if you’re unsure about any aspect of the inspection process, it’s always best to consult a professional mechanic.
To effectively clean your trailer bearings, start by carefully removing all old grease and debris. This process is crucial for ensuring optimal performance and longevity. Begin by using a clean cloth or paper towel to wipe away excess grease. For stubborn residue, employ a putty knife or scraper, being cautious not to damage the bearing surfaces.
Once the bulk of the old grease is removed, it’s time to employ cleaning solutions. Here’s a comparison of common cleaning methods:
Method |
Pros |
Cons |
---|---|---|
Solvent bath |
Thorough cleaning, removes all residue |
Requires proper disposal, can be harsh |
Soap and water |
Eco-friendly, readily available |
May not remove all grease, risk of rusting |
Specialized bearing cleaner |
Designed for bearings, effective |
More expensive, may require special handling |
Regardless of the method chosen, ensure thorough cleaning of all bearing components, including the races and cages.
After cleaning, proper drying is essential to prevent rust and ensure effective re-lubrication. Follow these steps:
With your bearings now clean and dry, they’re ready for the next crucial step in maintenance: proper lubrication. This process will ensure smooth operation and protect against wear and corrosion.
Selecting the appropriate grease is crucial for maximizing the lifespan of your trailer bearings. Shop premium-grade greases to keep your bearings in top condition, no matter the environment. Consider the following factors when choosing a lubricant:
Here’s a comparison of common grease types:
Grease Type |
Temperature Range |
Water Resistance |
Load Capacity |
---|---|---|---|
Lithium |
-20°F to 300°F |
Good |
Moderate |
Calcium |
-10°F to 250°F |
Excellent |
Low |
Synthetic |
-40°F to 400°F |
Very Good |
High |
To ensure optimal lubrication:
Over-greasing can be as detrimental as under-greasing. Signs of over-greasing include:
Re-lubrication intervals depend on several factors:
As a general rule, re-lubricate your trailer bearings:
Proper lubrication is key to extending the life of your trailer bearings. By choosing the right grease, applying it correctly, and maintaining an appropriate re-lubrication schedule, you’ll significantly reduce wear and tear on your bearings. Next, we’ll explore the correct installation and adjustment techniques to further enhance your bearing’s longevity.
Proper tension is crucial for optimal bearing performance. Follow these steps:
Now that we’ve covered correct installation and adjustment, let’s explore how to protect your trailer bearings from environmental factors.
Quality seals and caps are crucial for protecting your trailer bearings from environmental factors. They act as the first line of defense against contaminants that can cause premature wear and damage. Here’s a comparison of different seal and cap options:
Type |
Protection Level |
Durability |
Cost |
---|---|---|---|
Rubber Seals |
High |
Medium |
Low |
Metal Caps |
Very High |
High |
Medium |
Plastic Caps |
Medium |
Low |
Very Low |
When selecting seals and caps, consider:
Water is one of the biggest threats to trailer bearings. Implement these strategies to enhance water resistance:
Temperature fluctuations can significantly impact bearing performance. To mitigate these effects:
By implementing these protective measures, you can significantly extend the life of your trailer bearings. Next, we’ll explore towing best practices that further contribute to bearing longevity.
Proper weight distribution is crucial for maintaining the health of your trailer bearings. An unbalanced load can cause uneven wear and tear, potentially leading to premature bearing failure. To ensure optimal weight distribution:
Here’s a quick guide to weight distribution:
Position |
Ideal Weight Percentage |
---|---|
Front |
40-45% |
Middle |
30-35% |
Rear |
20-25% |
Overloading your trailer puts excessive stress on the bearings, significantly reducing their lifespan. Always adhere to your trailer’s maximum weight capacity and consider the following:
Excessive speed can cause bearings to overheat and fail. Follow these guidelines:
Long trips can cause bearings to heat up significantly. Implement these cooling techniques:
By following these best practices, you can significantly extend the life of your trailer bearings and ensure safer, more reliable towing experiences. Next, we’ll explore when it’s time to replace your trailer bearings despite your best maintenance efforts.
When it comes to trailer bearings, knowing when to replace them is crucial for maintaining safety and performance. Get in touch with our team for professional advice or service. Here are key indicators that your trailer bearings need replacement:
Sign |
Description |
Urgency |
---|---|---|
Grinding noise |
Indicates severe damage |
Immediate replacement |
Squealing |
Possible lack of lubrication |
Soon, within weeks |
Rumbling |
Early stages of wear |
Plan replacement in coming months |
Uneven tire wear |
Can be caused by worn bearings |
Check and replace if confirmed |
Selecting the right replacement bearings is essential for longevity and performance:
Deciding between professional and DIY replacement depends on your skill level and tools:
Professional replacement:
DIY replacement:
Whichever method you choose, always prioritize safety and follow manufacturer guidelines for the best results.
Maintaining your trailer bearings is crucial for ensuring safe and smooth towing experiences. By following the essential steps outlined in this guide, including regular inspections, proper cleaning, correct lubrication, and careful installation, you can significantly extend the life of your trailer bearings. Remember to protect your bearings from environmental factors and adopt towing best practices to further enhance their longevity.
Don’t wait until you’re stranded on the side of the road with a failed bearing. Take proactive steps to care for your trailer bearings, and they’ll reward you with reliable performance and peace of mind on your journeys.
With over 20+ years of experience, our team are always ready to assist with any enquiries you may have
Our products are designed, manufactured and rigorously tested to comply with Australian Design Rules
Orders are ready to be shipped Australia wide or picked up via Click & Collect typically within one to two business days
Rest assured we offer hassle free change of mind returns for all our products. See our Returns Policy for more information on this.
Need a hand or more information? We would love to hear from you. You can get in touch with us through phone, email or by filling out the following enquiry form. One of our team members will be in touch shortly after.
Need a hand? We would love to hear from you. You can get in touch with us through phone, email or by filling out the following enquiry form. One of our team members will be in touch shortly after.